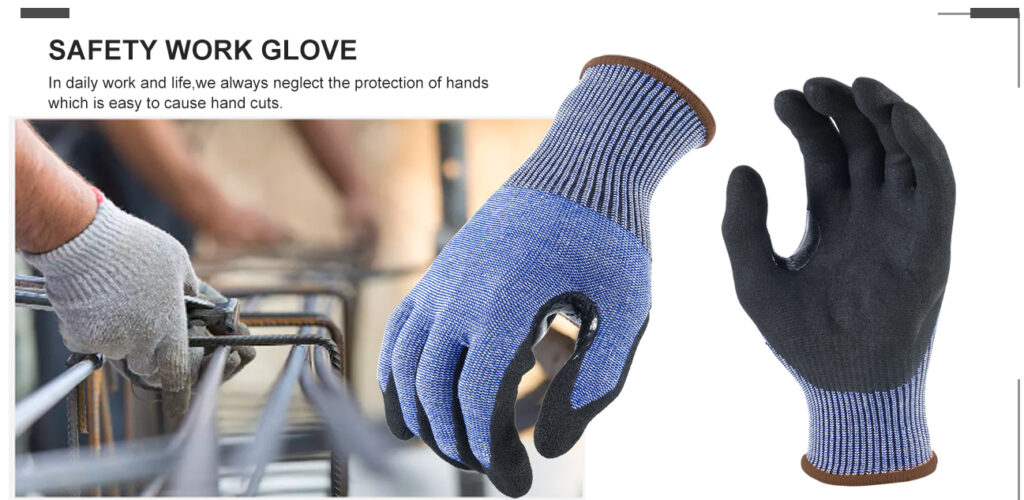
Industrial safety gloves1 are essential for protecting workers from a range of hazards, from chemicals to sharp objects and extreme temperatures. However, even the best gloves have a limited lifespan, and understanding when to replace them is crucial for maintaining safety. In this article, we'll explore how often safety gloves should be replaced, factors that influence glove wear, and guidelines for knowing when it’s time to change your gloves.
Replacing safety gloves on time is essential for ensuring the safety and comfort of workers. Worn-out gloves can compromise protection, leading to serious accidents.
Industrial gloves undergo wear and tear over time, and their ability to protect you diminishes with each use. But how do you know when to replace them? Let's dive into this topic to help you determine the right replacement schedule for your gloves.
How often should safety gloves be replaced?
The frequency at which safety gloves should be replaced depends on the type of gloves, the work environment, and how often they are used. Generally, gloves should be replaced when they show signs of wear or damage that could compromise protection.
1. General Recommendations
For most gloves used in industrial environments, it’s recommended to replace them every 6 to 12 months. However, this can vary depending on the level of exposure to hazards and the type of work being done.
2. Check for Visible Damage
Always inspect gloves regularly for signs of damage such as tears, punctures, or thinning material. If any part of the glove shows visible wear, it should be replaced immediately.
3. Use-Dependent Factors
In environments with high-risk exposure—such as construction sites, chemical plants, or heavy machinery—gloves may need to be replaced more frequently, possibly after each use if they are heavily contaminated or damaged.
What is the lifespan of safety gloves?
The lifespan of safety gloves varies based on several factors, including the type of glove, the materials used, and how they are maintained. On average, most industrial gloves can last anywhere from 3 to 12 months with regular use. Here are some factors that affect glove lifespan:
1. Material Durability
- Leather Gloves: Leather gloves2 can last 6 to 12 months, depending on how frequently they’re used and how well they’re maintained. Leather is durable, but exposure to moisture, extreme temperatures, and abrasions can shorten their lifespan.
- Nitrile and Rubber Gloves3: These gloves are typically replaced every 3 to 6 months in industrial settings. Nitrile gloves offer excellent chemical and puncture resistance, but they can degrade over time due to prolonged exposure to chemicals and oils.
- Cut-Resistant Gloves4: Cut-resistant gloves made from materials like Kevlar®5 or steel mesh usually last 6 to 12 months depending on the intensity of use. Heavy-duty tasks will wear out gloves faster.
2. Frequency of Use
The more often gloves are used, the shorter their lifespan. Gloves that are exposed to heavy wear, chemicals, or extreme conditions will need to be replaced more frequently.
3. Maintenance
Proper cleaning and maintenance can extend the life of gloves. For example, leather gloves can last longer if they are regularly cleaned and conditioned. Similarly, rubber gloves should be washed and dried after each use to prevent degradation from chemicals.
How often should you change work gloves?
Changing work gloves depends on both the frequency of use and the type of work being done. For tasks involving high risks, gloves should be replaced as soon as they show signs of wear or when they are no longer effective in providing protection.
1. After Heavy Exposure
If gloves are exposed to chemicals, oils, or abrasives, or if they are used in extreme heat or cold, they should be replaced more often. For example, gloves used in welding or metalwork may need to be replaced after each job, especially if they are visibly worn or contaminated.
2. At the First Sign of Damage
If a glove has a tear, hole, or any form of visible damage, it should be discarded immediately. Even small damage can reduce the glove’s protective capability.
3. When Protection Decreases
If you notice a decline in the glove’s performance—whether it no longer offers a strong grip, no longer resists punctures, or is no longer waterproof—it’s time to change gloves.
How often should a worker change gloves?
Workers should change their gloves as often as necessary to maintain safety. The exact frequency depends on the job and the condition of the gloves. Here are some general guidelines:
1. Daily Use
If gloves are used continuously throughout a shift, workers should inspect and change them at least once per day. In industries like food processing6 or healthcare, where gloves come into direct contact with hazardous substances or pathogens, they should be changed more frequently, often after each task or after exposure to contaminants.
2. High-Risk Environments
In high-risk environments, gloves should be replaced after each task or use, especially if they are exposed to chemicals, sharp objects, or machinery. For example, workers in construction or automotive repair should inspect gloves after each task and replace them if necessary.
3. Personal Comfort
Even if gloves aren’t visibly damaged, workers should replace them when they feel uncomfortable or less effective. Sweaty or uncomfortable gloves can distract workers and lead to decreased safety. Additionally, gloves that lose their grip or flexibility can be hazardous, especially when handling tools or machinery.
What are the guidelines for changing gloves?
There are several guidelines you can follow to ensure that gloves are changed properly and at the right time:
1. Follow Industry-Specific Standards
Different industries have different standards for glove replacement. For example, OSHA7 recommends that gloves be replaced if they are exposed to hazardous chemicals or if they show visible signs of damage. Similarly, healthcare organizations may have more stringent guidelines regarding the frequency of glove changes to prevent contamination.
2. Regular Inspections
Set up regular glove inspections to check for signs of wear and damage. A worker should inspect their gloves at the beginning and end of each shift and after any potentially hazardous task.
3. Replace When Performance Diminishes
If gloves are losing their ability to provide grip, cut resistance, or chemical protection, they should be replaced immediately. Any glove that no longer performs its intended function can compromise safety.
4. Consider the Type of Hazard
Gloves should be replaced based on the type of hazard they are protecting against. For instance, gloves used in chemical handling8 should be replaced more frequently due to the risk of degradation from chemicals. Similarly, gloves used for cut protection should be replaced once they become visibly worn, as they can no longer provide adequate protection.
Conclusion
Replacing industrial safety gloves on time is essential for maintaining workplace safety and preventing injuries. While the lifespan of gloves varies depending on the type and usage, regular inspections and adherence to industry standards will help ensure that workers are always protected. Remember, gloves that are worn out or damaged no longer provide the level of protection you need, so it’s important to replace them promptly for maximum safety on the job.
Footnotes
-
This resource will explain the importance of industrial safety gloves, including their role in protecting workers from various workplace hazards such as chemicals, sharp objects, and extreme temperatures.
-
Leather gloves, often used in various industrial settings, can last anywhere from 6 to 12 months, depending on usage and maintenance. Proper care can prolong their lifespan.
-
Rubber gloves, which are commonly used in industries dealing with chemicals and oils, need to be replaced regularly due to degradation from exposure to these substances.
-
Cut-resistant gloves offer protection against sharp objects, and their durability depends on the intensity of use. These gloves should be replaced once they are visibly worn.
-
Kevlar® is a strong, cut-resistant material commonly used in protective gloves. Understanding its properties helps explain why cut-resistant gloves made from Kevlar® are a durable choice in hazardous environments.
-
In food processing, gloves should be replaced frequently to maintain hygiene and prevent contamination. This resource will outline why frequent glove changes are necessary in these environments.
-
The official OSHA guidelines provide specific recommendations regarding the replacement of safety gloves in industrial settings, ensuring compliance with workplace safety standards.
-
Gloves used in chemical handling require more frequent replacement due to the potential for chemical degradation, ensuring workers remain protected from harmful substances.